Share and Follow
“We had to do some interior stuff like the bathroom and the kitchen,” Mattias says. “But pretty much the house was there: the windows, the roof, everything.”
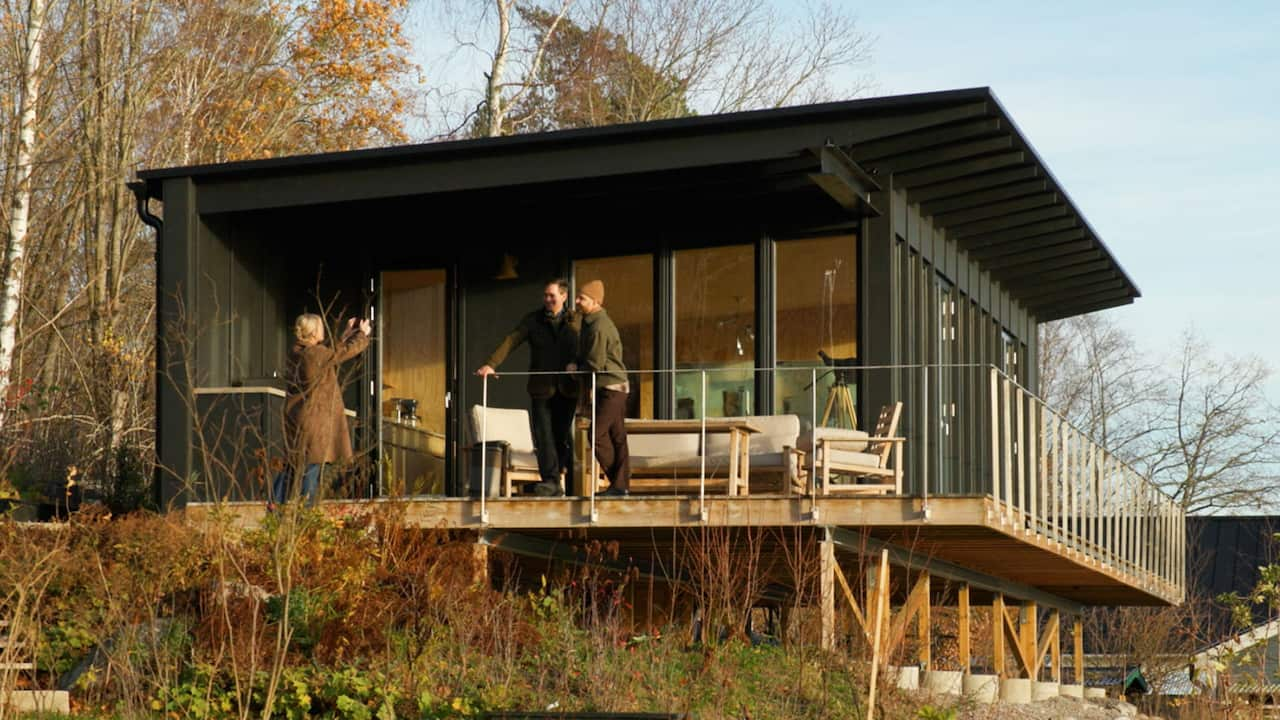
Rickard Rundqvist and Mattias Borg’s home is a 70-square-metre one-bedroom, one-bathroom house with a sauna overlooking the Baltic Sea. Source: SBS / Colin Cosier
Historically, prefab has had bad rap. In Australia, it’s often associated with school demountables and mining dongas. And while the process can be thought of as low-quality and unoriginal, Rickard and Mattias say their home was designed to reflect their vision in collaboration with architects at the construction firm.
Although the couple doesn’t disclose the total costs, they say they did save money because less labour was involved.
“I think it’s just the most practical way of doing it. [We saved] time and money, [it was] way more cost efficient,” Rickard says.
House factories
Across the country, so-called ‘house factories’ churn out up to four apartments a day, equipped with insulation, electricity and plumbing and ready for assembly on site.
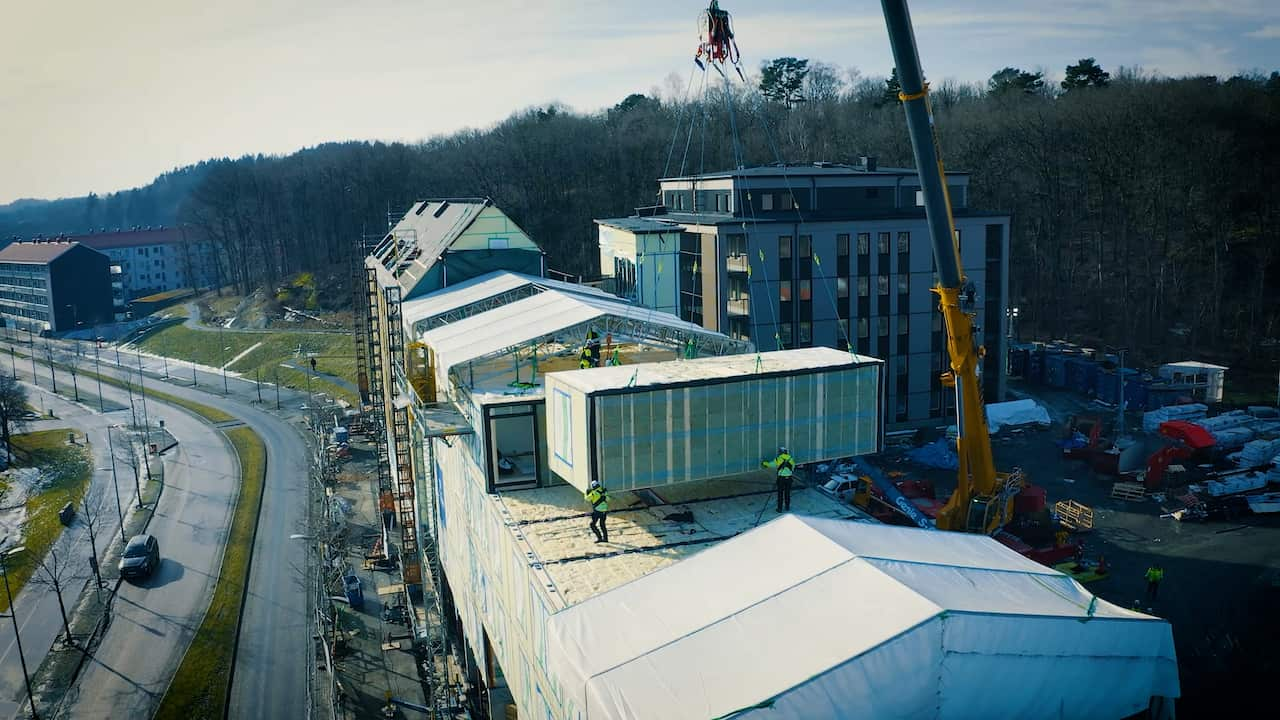
Across Sweden, so-called ‘house factories’ build four apartments a day, equipped with insulation, electricity and plumbing and ready for on-site assembly. It takes a few months to put together an apartment building. Source: SBS / Colin Cosier
Modelled off the car industry, the factories have their operations centred around one main production line, with robots working alongside humans for speed and efficiency.
“When we’re talking wood today, we’re talking mass timber, or engineered timber,” architect Oskar Norelius says.
“It’s a good material, it’s very lightweight, it’s quite easy to work with in a factory,” he says.
‘We were able to land one’
The couple was living with Maja’s parents and thought it would take them years to find an affordable home of their own. But then came an influx of prefab apartments in their desired area.
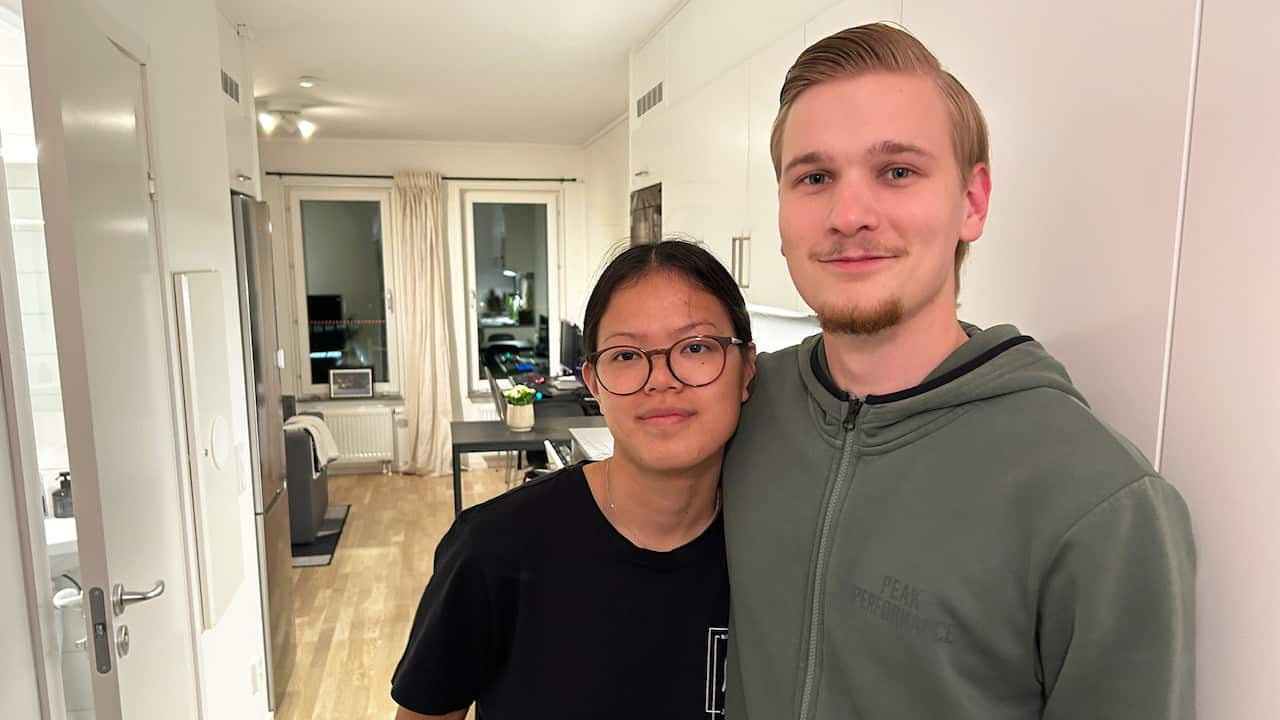
A young couple Maja and Kilian were able to secure a rental studio in a new apartment complex that was built in ten months using the prefab method. Source: SBS / Colin Cosier
Their complex is made up of 96 apartments, all built in a factory.
“There were I think 60 apartments published at once. And since they did not have 60 people applying for them, they took all of the possible tenants and gave them the opportunity to rent these apartments,” Kilian says.
Can Australia build the Swedish way?
In its latest budget, Labor pledged almost $50 million dollars to support modular home construction. State governments are also throwing money at the industry.
“If you want to make a prefabricated housing business, it does require a large amount of capital to set it up. It requires planning, it requires knowledge of manufacturing, and that can take some time.”
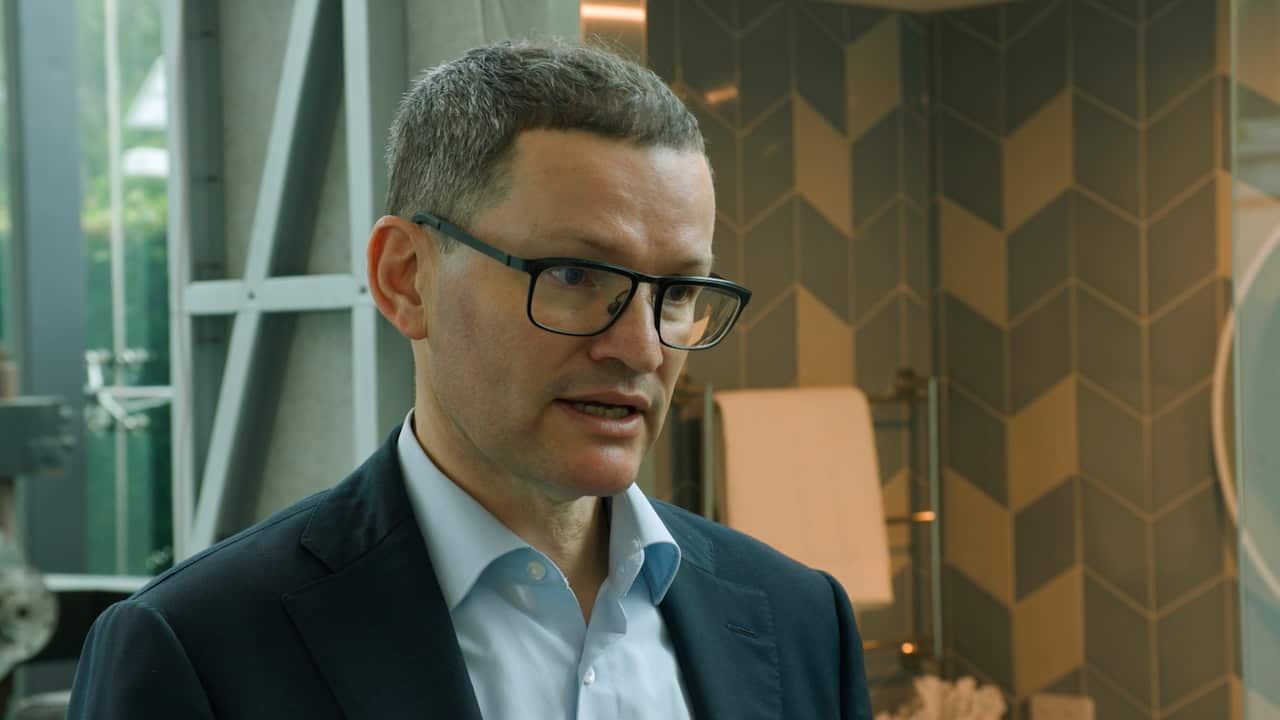
Mathew Aitchison of Monash University says there are many lessons Australia can learn from Sweden in prefab construction. Source: SBS / Colin Cosier
And he says, to be both profitable for businesses and affordable for consumers, you need to build at scale.
And in Australia, that won’t happen overnight.
“There is a lot of interest in [prefab] in Australia at the moment and that’s coming from industry and government. There are many lessons we can learn from Sweden, and I think the future of construction is a future of industrialisation.”
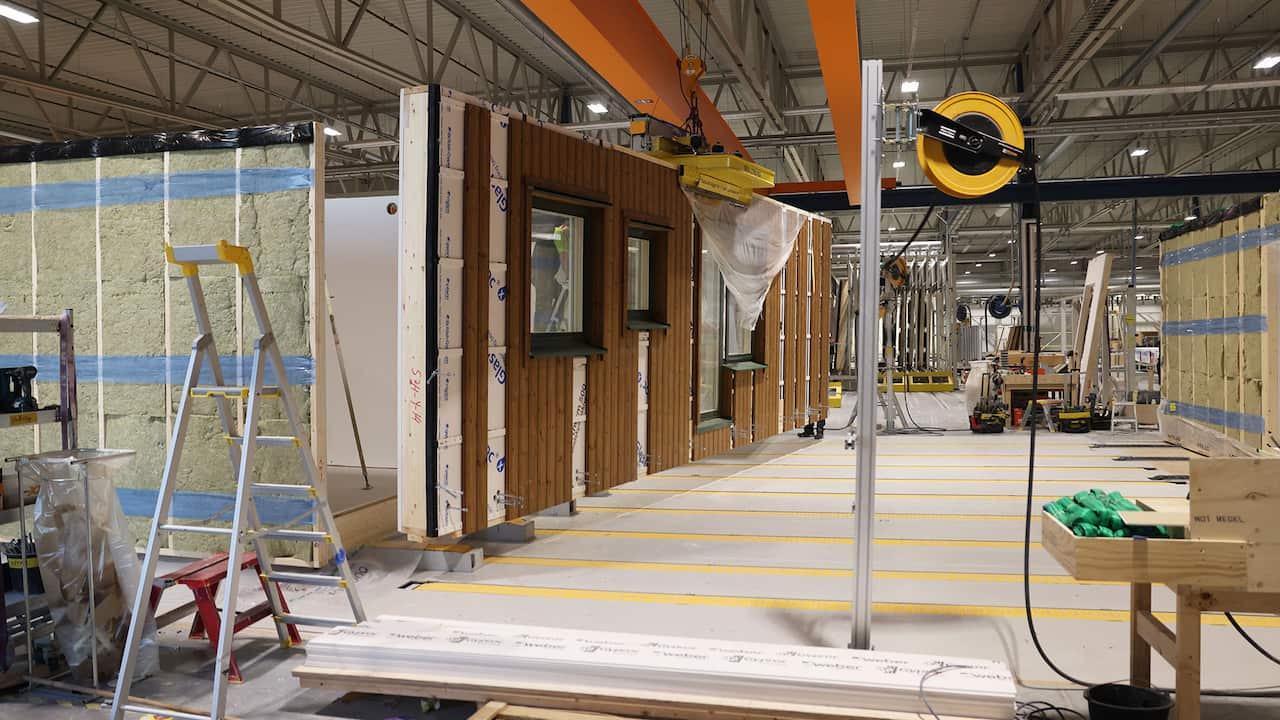
Prefab makes up less than 10 per cent of construction in Australia, with bathroom pod manufacturing being the most developed part of the industry. Source: SBS / Colin Cosier
Speaking from a modular bathroom factory on the NSW Central Coast, where they make around 16 bathrooms a day, Aitchison says it’s this type of prefab that is taking off.
“[Prefab] can be what we want it to be. So, to me, speeding up that building time using less materials, less waste, less labour – that’s innovation.”